Table of Contents
Las cadenas de oruga, conocidas también como enlace de oruga, pertenecen al tren de rodaje de diversos tipos de maquinarias pesadas, su principal función es conectar el movimiento de avance que es producido por los pedales hacia ruedas de características motriz con el objetivo que provocar un movimiento continuo hacia adelante, se emplea en maquinaria pesada a oruga como por ejemplo excavadoras y topadoras
La maquinaria pesada de oruga cuenta con un mecanismo que evita que las ruedas motrices se apoyen directamente en el suelo, por lo cual se encuentran unidas y engranan con cojinetes de deslizamiento que producen que los eslabones se articulen entre sí para formar las cadenas. En la zona exterior del eslabón se conecta una zapata mediante tornillos, con lo cual la máquina se va a poyar y tener agarre con el suelo. Generalmente las zapatas llevan garras para poder tener un agarre óptimo con el suelo, ocasionando que todo el peso descanse sobre las cadenas, este tipo de maquinaria es el más recomendado para poder operar en todo tipo de terreno.
Con este mecanismo, cuando se produce un giro de las ruedas motrices gracias a la unión en las cadenas produce el movimiento de la máquina. Los dientes de las ruedas motrices recogen los eslabones que retornan al suelo sobre las ruedas guiadoras que cumplen la función de guiar las cadenas para que retornen al suelo generando que continuamente un movimiento delantero.
ESTRUCTURA DE LAS CADENAS DE ORUGA
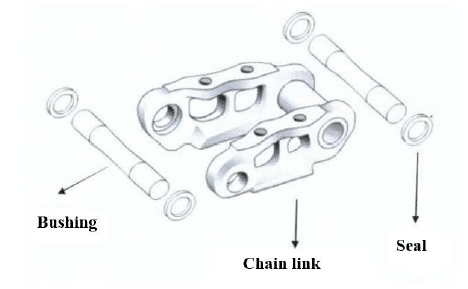
A diferencia de las excavadoras, los buldóceres requieren un mayor esfuerzo de tracción, por lo cual sus eslabones en consecuencia están sometidos a esfuerzos mucho mayores que los de otros tipos de equipos.
Las cadenas de orugas están conformadas por:
- Eslabones
- Pasadores
- Bujes
- Sellos
- Pernos de sujeción
- Zapatas
ESLABÓN
Los eslabones generalmente tienen una forma inusual, el área más importante del eslabón es aquella que va a estar en contacto con el suelo, la superficie de rodamiento, debido a que se requiere que tenga propiedades que evitan el desgaste muy rápido.
Debido a la naturaleza de la operación de la maquinaria el eslabón se encuentra sometido a desbaste y esfuerzo al contacto con el suelo. Por otro lado, también debe soportar cargas elevadas de los rodillos en función que la máquina avanza y retrocede durante la operación de esta.
Para prolongar el tiempo de vida útil de los eslabones se fabrican en materiales con alta resistencia en el área de superficie rodante para poder cumplir los requisitos más críticos. El montaje del eslabón, el buje y el pasador se insertan en los respectivos costados y extremos opuestos, asegurando que el pasador y el buje no se escapen del eslabón, se emplea un ajuste a presión. El área de contacto del eslabón con el suelo posee una mayor dimensión debido a que es sometida a presión, consiguiendo un ajuste más apretado. La superficie que se somete a mayor esfuerzo para mejorar su propiedad de dureza se efectúa un tratamiento térmico de temple para garantizar que el desgate que se produzca no sea tan desigual.
Existen dos tipos de montajes de eslabón:
– Tipo de eslabón maestro
El eslabón está dividido en secciones y conectado empleando pernos, es recomendable debido a su facilidad de montaje para la zapata de oruga.
– Tipo de pasador maestro
En el montaje se requiere extraer el pasador para reemplazarlo, el pasador maestro está biselado y el buje maestro es de tamaño menor que el buje regula, para poder extraerlo con facilidad de su posición usual entre los eslabones.
BUJE
El buje requiere tener una resistencia al desgaste elevada, al igual que como característica relevante debe tener tolerancia y resistencia a la fatiga para otorgarle al buje a resistir los impactos de la rueda dentada. La superficie interior y exterior debido a su funcionamiento están sometidas a fricción y desgaste por lo cual se realiza un tratamiento térmico donde se templa la pieza para aumentar su durabilidad.
Usualmente la superficie externa del buje se desgasta de manera más rápida que la superficie interna, esto se debe a que está en contacto con la superficie de la rueda dentada que en operación ocasiona un martilleo, además que el material particulado de la tierra puede generar un desgaste mucho mayor. Se produce un desgaste adicional entre el pasador y la superficie interior del buje.
PASADOR
Se requiere que el pasador tenga la capacidad de soportar los esfuerzos de tracción contantes de los eslabones y que tenga una alta resistencia para evitar el desgaste. Es una pieza de suma importancia debido a que es la responsable de la unión de los eslabones. Además, que debido al peso propio del equipo se produce una fuerza de flexión elevada, por lo cual se diseña el pasador con una alta resistencia a la fatiga Existen 2 clases de pasadores, el pasador regular y el utilizado para reemplazo conocido como pasador maestro, el pasador regular tiene un diámetro mayor que el pasador maestro.
SELLO
El tiempo de vida de la oruga lubricado en aceite depende del tipo de sello, debido a que, si el sello se rompe o falla, el aceite se libera y permite que arena ingrese al buje acelerando el proceso de desgaste tanto del buje como del pasador. La tensión selladora comienza a disminuir a medida que el sello se desgasta, generando que el interior del buje y pasador se desgasten de manera más rápida en consecuencia de las fugas internas de aceite y las partículas de arena que ingresan.
LUBRICACIÓN ENTRE EL BUJE Y EL PASADOR
Lubricación por medio de sellado en aceite
El sello del eslabón de oruga sellada en aceite está conformado por un anillo sellador que evita la entrada de arena y anillo interno de carga y lubricación de aceite que genera una fuerza de compresión contra el sello. El anillo de carga se diseña para mantener la capacidad de sellado con elasticidad a medida que se comprime y empotra el eslabón.
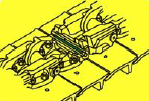
Lubricación por medio de sellado en grasa
A medida que el anillo sellador en el tipo de sellado con grasa se aplasta adquiere una función similar a la del anillo de carga para el tipo sellado en aceite.
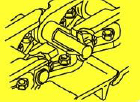
ZAPATA
Una analogía común de la zapata de maquinaria es la suela de un zapato común debido a que cumple básicamente la misma función, para cada tipo de terreno es necesario escoger un calzado con una suela adecuada, por ejemplo, para escalar no es adecuado utilizar un calzado con suela lisa. El efecto es igual en la maquinaria, si no se escoge la zapata correcta la máquina no podrá ganar tracción de manera óptima.
Ejemplificando, si en el caso de que una máquina esté operando en un terreno de caracteristicas arenosas es muy probable que la máquina resbale si no posee las zapatas adecuadas, generando que todo el conjunto del tren de rodaje disminuya su vida útil drásticamente. Por esa razón es extremadamente importante la correcta selección de zapatas para una operación óptima y para evitar tener que invertir más dinero en reparaciones futuras.
ESTRUCTURA DE LA ZAPATA DE ORUGA
La zapata de oruga se encuentra conectada a los eslabones usualmente empleando 4 pernos y 4 tuercas. Existe una gran variedad de zapatas con diversas anchuras y formas de garra. La zapata de oruga está conformada por una plancha la cual soporta el peso completo de la máquina, y una garra que tiene el objetivo de ejercer tracción en la superficie del terreno. Durante la operación, la zapata de la oruga debe vencer esfuerzos como el ocasionado por la fuerza de flexión, fuerza de fricción que genera desgaste y desgarramiento. Es por esto que las zapatas de orugas se diseñan para poder resistir elevadas cargas y con una resistencia al desgaste por fricción. En la etapa de diseño se realizan estudios y simulaciones para que en funcionamiento se evite que las rocas y arena queden atrapada entre las zapatas.
RECOMENDACIÓN PARA MANTENIMIENTO DE LA CADENA DE ORUGA
El mantenimiento requiere un tiempo relativamente prolongado por lo que se recomienda realizar un itinerario de mantenimiento previo para evitar interrumpir el funcionamiento usual del equipo, además que es necesario realizar inspecciones periódicas que lograrán prevenir que se requieran costosas reparaciones de los elementos del tren de rodaje.
El tren de rodaje representa un gran costo de la máquina, es prácticamente imposible evitar el desgaste a pesar de que el diseño y la calidad sean excelentes, sin embargo, comprender las causas del desgaste en combinación con métodos de inspección y buenas prácticas de mantenimiento lograrán aumentar la vida útil del tren de rodaje.
Los puntos en los cuales la inspección suele ser más importante son:
- Paso del eslabón: Se mide la relación que existe entre el desgaste del diámetro interior del buje y el exterior del pasador.
- Altura de la superficie de rodamiento del eslabón: Se mide el grado de desgaste en la superficie de rodamiento del eslabón.
- Diámetro exterior del buje: mide el estado de desgaste.
Los puntos en los cuales la inspección suele ser más importante son:
- Determinar si existen cuarteaduras en los eslabones
- Corroborar que los pernos de la zapata se encuentren apretados correctamente
- Inspeccionar si existe alguna fuga de aceite, en el tipo de eslabones sellados con aceite, se puede verificar por la apariencia, o por la temperatura entre el pasador y el buje.
En el mantenimiento programado de los eslabones de las orugas se deben cambiar los dientes de las ruedas dentadas para garantizar que el tiempo de vida útil del tren de rodaje sea mayor. Debido a que si solamente se cambian los eslabones de la oruga, el desgaste existentes en los bujes será mayor en ese momento , por lo cual en términos económicos se recomienda modificar ambos a la vez.
AJUSTE DE HOLGURA DE LA ORUGA EN LAS CADENAS DE LA EXCAVADORA
Cuando se inspeccionan máquinas tipo oruga es común notar que las cadenas se encuentran apretadas de una manera exagerada, lo cual genera un mayor desgaste en los bujes , ruedas dentadas y catarinas provocando que la vida útil del conjunto se reduzca. Es común que en ocasiones los rodillos, las zapatas y los eslabones se encuentren en un estado óptimo para operación , pero por otro lado los bujes y las catarinas están al límite del desgaste.
Existen 2 escenarios posibles, que la tensión de oruga sea demasiada baja o muy apretada, en el caso de de tensión muy baja genera que los bujes se monten sobre la rueda dentada en operación, también existe la posibilidad que la cadena salte por encima del borde de la rueda guía.
Cada equipo tiene un valor de tolerancia que se especifíca, por lo cual la holgura de la cadena debe regirse por lo recomendado por el fabricante antes de realizar el ajuste.
Para realizar el ajuste es necesario levantar la máquina con el brazo hasta que la cadena de la parte levantada quede colgando sobre el suelo. Encienda el equipo para que la oruga entre en funcionamiento logrando como mínimo una vuelta completa. Se requiere medir la distancia que existe entre la superficie de la cadena y la superficie del rodillo inferior en el centro de la oruga. En el caso de que la holgura esté fuera de los rango de tolerancia recomendados generalmente se realiza el apriente con una grasera. Si la cadena está muy apretada, es decir holgura demasiado pequeña, también se requiere modificar el ajuste. En casi todas las excavadoras existe un perno de alivio montado en el lugar donde se requiere aplicar la grasa.
TIP DE SEGURIDAD
Para poder trabajar en las orugas verifique que el equipo no se pueda mover, antes de realizar cualquier cambio en el equipo se debe leer el manual de operación y mantenimiento de la máquina para obtener la información correcta sobre la realización del ajuste. Como regla básica de mantenimiento se requiere que al menos tres miembros del cuerpo deben estar en contacto con los escalones o barras de apoyo , este requisito es indispensable debido a que la fuerza aplicada en los tensores de la oruga son bastante elevadas y pueden presentar un riesgo a la integridad física del operario.
CONSEJOS PARA MEJORAR LA VIDA ÚTIL DEL TREN DE RODAJE
Un consejo clave es seguir estrictamente el plan de mantenimiento recomendado en la sección previa, respecto a la vida útil de las piezas del tren de rodaje se recomienda seguir las siguientes instrucciones para poder incrementar la vida útil:
- El equipo debe trabajar con una velocidad apropiada
- Verifique que la tensión de las cadenas de orugas sea correcta
- No es conveniente que el equipo realice giros de forma aguda
- Evitar girar en una misma dirección
- Realice una limpieza periódica para retirar el lodo que se acumula en las piezas del tren de rodaje
- Se recomienda estacionar la máquina en superficies planas.
- Reemplace inmediatamente si es necesario: sellos, eslabones rotos o muy desgastados y anillo de empaque interno para mantener el axial adecuado.
PREGUNTAS & RESPUESTAS
¿Qué sucede si el conjunto de zapata se instala en sentido contrario?
Existen varias consecuencias tales como:
- Los bujes de los eslabones de las orugas y los dientes de las ruedas dentadas acelerarán su proceso de desgaste
- Si la zapata se coloca en la dirección opuesta, los dientes de la rueda dentada se acoplarán en el buje del eslabón en la parte inferior de la rueda dentada, por otro lao cuando se instala en la posición adecuada el acople se produce en la parte superior de la rueda.
- Debido a la posición de la zapata, la arena y tierra podrán ingresar entre el buje y los dientes de la rueda dentada generando un desgaste en ambos.
- Debido a que el eslabón de la oruga se enroscar a la tierra de produce un movimiento no deseado que reduce de manera significativa la fuerza de tracción.

En la figura A la zapata está instalada correctamente, mientras que en la figura B se evidencia que la instalación fue incorrecta, por lo que el movimiento final no es el esperado.
¿Por qué se gastan los bujes de manera más rápida cuando la máquina retrocede?
Cuando el equipo está en funcionamiento y retrocede se produce una fuerza de tracción que genera mayor desgaste. Los bujes y dientes de la rueda dentada mantienen un contacto mutuo en la parte superior de la rueda dentada. Cuando la máquina retrocede, se incorpora una fuerza de tracción elevada en la pieza, lo que acelera el desgaste.
¿Qué tipo de instrumentos se requieren para hacer las inspecciones en la cadena de orugas?
Depende del tipo de inspección que se requiera, algunas como ya se mencionó requieren de una inspección visual previa. Además, que previo a la realización de cualquier tipo de inspección se necesita realizar una limpieza para retirar el lado o la arena de la cadena.
Por otro lado, para cada tipo de inspección se requiere un instrumento diferente, a continuación, se mencionan los instrumentos empleados en las mediciones más comunes:
- Medir el desgaste en la altura de los eslabones se necesita de una regla, un calibrador vernier o un profundímetro
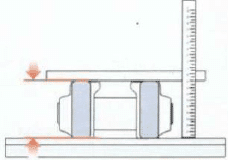
- Medir el desgaste del buje se emplea un calibrador vernier tomando mediciones de los diámetros externos en posiciones diferentes midiendo dos diámetros, D1 y D2, para registrar la diferencia entre los valores y corroborar el grado de desgaste.
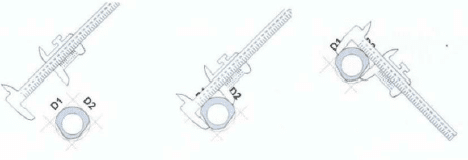
- Medición de luz entre los eslabones de la cadena se emplea galgas de medición, para medir la luz entre el interior y exterior del elemento, se mide dos puntos y se promedia.
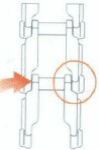
- Medición del ancho de la rueda dentada, se toma un registro de ancho de diente en la rueda dentada y se obtiene un promedio.
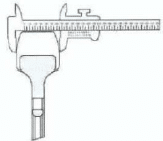
- Medir del perfil de los dientes de la rueda, para realizarlo se necesita una limpieza profunda previa, se debe emplear galgas de medición de desgaste de las ruedas se toman lecturas, se requiere realizar un registro para dos dientes diferentes y obtener un promedio.
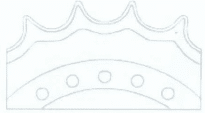
0 comentarios