Table of Contents
Para poder optimizar la vida útil del tren de rodaje es muy necesario conocer el estado de cada uno de los componentes, especialmente el estado de desgaste, ya que debido al desgaste que se produce en cada componente el tren de rodaje puede verse sobrecargado, al conocer el estado de los componentes se pueden tomar decisiones sobre el cambio o la reconstrucción de los mismo. Lo que permite que la vida útil se prolongue.
Existen diversos métodos, equipos y técnicas para poder conocer el estado de desgaste los componentes, como regla general para poder medir desgastes es necesario ser muy minucioso al realizar las medidas, en ocasiones serán necesarias varias medidas de las cuales se debe realizar un promedio para poder tener un valor más preciso.
Para cada elemento la medición y la técnica para medición del desgaste es diferente, ya que depende de la estructura, a continuación, se analizarán las mediciones a diversos componentes.
TÉCNICA DE MEDICIÓN
Existen dos técnicas de medición de los eslabones de pista, se puede realizar la medición con un medidor de profundidad o con un indicador de desgaste por ultrasonidos.
Con la técnica del medidor de profundidad se debe realizar la medición de la altura del eslabón desde la superficie del riel hasta la zapata de la oruga. La medición se realiza correctamente cuando se ubica fuera de los enlaces al final del pin de la pista. Se debe colocar el medidor de profundidad lo más cercano posible del extremo del pasado, verificando que los eslabones y la superficie de la zapata no tengan suciedad o elementos adheridos. La medición debe tener una precisión de 0,01 pulg. O 0,25 mm.
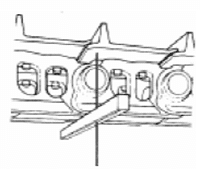
Por otro lado, con la técnica del indicador de desgaste ultrasónico mida la distancia desde la superficie del riel hasta el orificio del buje, debe colocar la sonda en el enlace encima de la línea central del buje y deslizar la sonda a lo largo de la superficie de la banda de rodadura para realizar la lectura más pequeña.
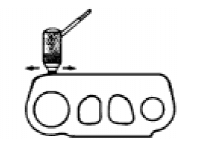
LÍMITES DE DESGASTE
Para poder establecer los límites de desgaste del eslabón se debe comenzar estableciendo un desgaste permisible que sea igual a una fracción del espacio libre entre el eslabón y el rodillo. En ciertas máquinas, este espacio se encuentra entre el saliente del pasador de enlace y la brida del rodillo. Por otro lado, en otro tipo de máquinas el espacio libre se encuentra entre el buje y las bridas internas de un rodillo de doble brida.
En el caso que se tenga un eslabón 100% desgastado con un rodillo en igual situación, las bridas de los rodillos estarán en contacto con los salientes del pasador del eslabón o con el buje, a partir del 100% en adelante el desgaste del pasador del eslabón falla reduciendo de esta manera la retención del pasado, además que el desgaste de los bujes puede ocasionar que se produzcan grietas.
LÍMITES DE DESGASTE: MAYORES Y MENORES
La resistencia restante a la fisuración indica cual es el límite de desgaste que soportan los eslabones de las cadenas selladas y lubricadas.
En las mediciones ultrasónicas se mostrarán tablas que demuestran que el riel de enlace siempre es más grueso lo que conlleva a que sea más resistente a la grietas en la columna de menor desgaste permisible en comparación con la columna de mayor desgaste permisible. Su correcta selección de la columna de desgaste óptima permisible maximizará la vida útil del eslabón y evitará que se agriete. La resistencia al agrietamiento depende de una serie de factores, entre las cuales destacan la posición de la rueda dentada (alta o baja), las condiciones del suelo donde se opere, la vida útil del eslabón y el tipo de operación que se realice.
PROCEDIMIENTO DE MONTAJE Y APRIETE
La correcta secuencia de montaje y apriete, permitirán asegurar que el eslabón maestro tendrá una vida útil de acuerdo con lo establecido por el fabricante, además que se asegura la integridad de la unión atornillada, por lo cual es necesario seguir correctamente el procedimiento especificado. Debe considerar que los valores del ángulo de giro de torsión de cinco dientes y de un solo diente son diferentes ya que los pernos tienen roscas diferentes.
- Previo a la instalación de la pista, se requiere hacer una limpieza en el punto de conexión del enlace maestro, verificar que no presente ningún tipo de daño, remueva toda la pintura.
- . Se debe aplicar un compuesto antiadherente a las roscas de los pernos, el cuerpo, la cara de la arandela y las áreas de contacto de los pernos en la zapata durante el montaje.
- Junte los eslabones maestros y Cerciórese de la alineación de los orificios para los pernos maestros. Instale un perno maestro en cada enlace. Cuando se giren con la mano, los pernos no deben presentar ninguna resistencia y deben girar fácilmente en las roscas.
- Retire los tornillos. nstale la zapata de cadena maestra y los 4 pernos maestros. Instale la zapata de cadena maestra y los 4 pernos maestros.
- Apriete los pernos maestros, las indicaciones del torque debe encontrarlas en el manual de equipo.
BUJE DE LA CADENA SELLADA Y LUBRICADA
TÉCNICA DE MEDICIÓN
Para poder realizar una medición el buje de la cadena es el componente más relevante. Se puede realizar de 3 maneras, cada método emplea herramientas diferente. Usted debe consultar para para saber qué método es el más adecuado en su caso, ya que por ejemplo la herramienta de medidor de profundidad brinda únicamente el desgaste en función de la posición vertical.
1. MÉTODO DE INDICADOR DE DESGASTE ULTRASÓNICO
Se considera que entre los métodos expuestos este es el más preciso debido a que realiza la dimensión justamente en la dimensión más crítica que es el espesor de la pared del buje, se realiza deslizando lentamente la sonda alrededor de los lados de transmisión inverso, vertical y delantero, es necesario que sea la dimensión más pequeña debido a que esta indica el desgaste.
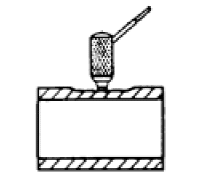
2. MÉTODO CALIPER
En este método se realiza la medición del diámetro del buje, es estrictamente necesaria una limpieza y realizar la técnica adecuadamente debido a que por una mala medición el valor de diámetro puede variar mucho del valor real llevando a la conclusión de que el desgaste ha sido muy acelerado, los errores más comunes de esta medición son:
Calibradores demasiado apretados: los calibradores que están demasiado apretados lo que genera que la medición sea menor a la real.
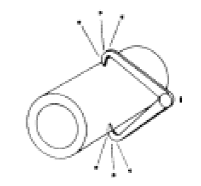
Calibradores en ángulo incorrecto con respecto al eje del buje: Provocarán que se tenga una medición mayor que la real.
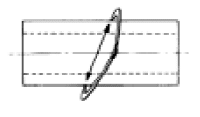
Calibradores que no se deslizan hacia adelante y hacia atrás en la posición que se va a medir: La lectura final será menor a la real.
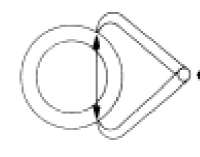
El buje no se limpió bien antes de la medición: si la superficie del buje no está limpia, la medición será mayor a la original debido a los residuos adheridos.
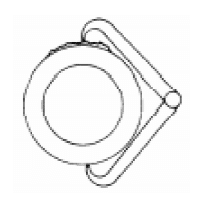
Calibradores no colocados en la parte más desgastada del buje:En el caso de que el calibrados este colocado de esta manera el valor medido será menor.
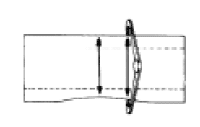
Se recomienda que para hacer la medición de desgaste de los bujes estén extraídos de la pista, la medición debe tener una precisión de ± 0.01 pulg. (± 0,25 mm).
3. MÉTODO DEL MEDIDOR DE PROFUNDIDAD
Emplea el mismo calibrador de profundidad que se utiliza en el caso de los enlaces. Este es un método más libre de errores en comparación con otros, sin embargo, puede no ser 100% preciso y estar sujeto a pequeñas diferencias dimensionales. Además, es una técnica que requiere mucho cuidado y precisión por parte del medidor. Entre los errores más comunes se encuentran:
- Componente sucio
- La base del medidor de profundidad está incorrectamente colocada con respecto a la longitud del buje.
- La sonda del medidor de profundidad no está colocada correctamente, por lo cual no forma un ángulo perpendicular o de 90 ° con la zapata.
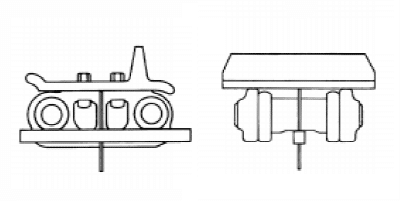
DESVENTAJAS DEL MÉTODO DEL MEDIDOR DE PROFUNDIDAD
Es imposible realizar una medición del desgaste del lado de la transmisión hacia atrás o hacia adelante lo cual es sumamente necesario para muchas aplicaciones.
VENTAJAS DEL MÉTODO DEL MEDIDOR DE PROFUNDIDAD
La parte trasera del buje podrá medirse después de girar el buje.
ZAPATA
TÉCNICA DE MEDICIÓN
En la zapata únicamente se puede medir el desgaste de la garra debido a que es para lo único que se tiene valores referenciales para comparación. El espesor de la placa se puede medir y realizar una comparación con una un componente nuevo para determinar el desgaste. En las zapatas se pueden emplear tanto el medidor de profundidad como el indicador de desgaste ultrasónico.
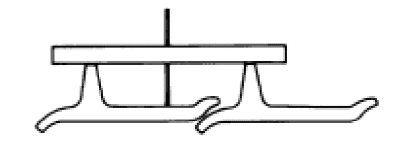
Empleando el indicador de desgaste ultrasónico la medición debe realizarse entre la punta de la garra y la parte inferior de la placa, se deben tomar 1/3 de camino desde el extremo de la zapata y la sonda se puede colocar en la parte superior o inferior. Las mediciones deben ser realizadas con una precisión de 0,02 pulg. o 0,5 mm.
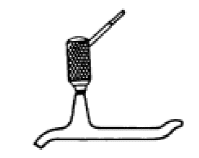
LÍMITES DE DESGASTE
Los límites de desgaste de las zapatas se basan en 3 criterios, se mencionan a continuación en orden de importancia:
- Zapata con resistencia a la flexión.
- La base de la zapata debe estar disponible disponible para fines de reuso.
- Capacidad restante de tracción-penetración de la zapata para lograr una capacidad de producción requerida.
RENDIMIENTO DE CAUSA Y EFECTO DE LA ZAPATA DE PISTA
La zapata es el componente que más se ve afectado por las condiciones de suelo y el manejo de la máquina debido a que se produce un mayor desgaste y se compromete la estructura disminuyendo su vida útil en comparación con cualquier otro de los componente en el sistema del tren de aterrizaje. Por otro lado, la correcta selección del tipo de zapata, al igual que de su ancho, tiene un impacto realmente grande en el rendimiento del equipo en general y del rendimiento de cada componente del tren de rodaje.
INSTALAR CORRECTAMENTE LOS ZAPATOS
En el caso que la zapata se afloje el principal motivo es que la tornillería de la zapata está mal apretada. A continuación, se muestra un pequeño procedimiento para apretar los pernos, se debe realizar una constante revisión cada 50 a 100 horas de funcionamiento del equipo, en ocasiones también depende de la experticia del operador, en el caso que sea necesario se debe descartar que el problema de la zapata sea por un mal apriete.
- Elimine todo el óxido y la pintura de las superficies de contacto de los eslabones y las zapatas.
- Lubrique las roscas de los pernos y las caras de las arandelas de los pernos.
- Apriete los pernos al torque especificado.
- Aplique a cada perno 1/3 de vuelta adicional.
Es necesario dar 1/3 de vuelta adicional al perno debido a que genera que se estire adecuadamente y mejora la retención, en el estiramiento del perno se produce una deformación permanente en el perno que asegura que se utilice la fuerza de sujeción máxima del perno.
RODILLO: RODILLOS CONVENCIONALES
TÉCNICA DE MEDICIÓN
Existen 2 posiciones de desgastes medibles en los rodillos, el primero en la banda de rodadura y el otro en la brida central. El desgaste de la banda de rodadura se puede determinar empleando una medición utilizando el medidor de profundidad desde la brida central de la superficie de la banda de rodadura. Se debe tomar una medición en ambos lados de la banda de rodadura central y se realiza un promedio de las medidas. El mayor error al medir el desgaste de la banda de rodamiento de los rodillos surge del desgaste en la brida central que altera el punto de referencia. Si usted considera que este desgaste existe debe intentar compensarlo en la medida tomada. Debe recordar que las medidas de desgaste de la banda de rodamiento de los rodillos aumentan disminuye a medida que se produce el desgaste de la brida central.
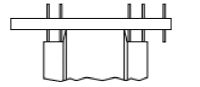
El desgaste de la brida central puede ser medido utilizando el indicador de desgaste ultrasónico. Mide el espesor de la brida central y debe tomarse directamente en el centro de la brida. Utilice el medidor de profundidad convencional para medir el desgaste en la superficie de la banda de rodadura, luego agregue el desgaste de la brida central a la medición del medidor de profundidad antes de determinar el porcentaje desgastado.
LÍMITES DE DESGASTE
Los límites de desgaste de la banda de rodadura de los rodillos se basan en dos criterios básicos: la capacidad de reconstrucción de la superficie de la banda de rodadura más el espacio entre la brida central y el buje de la oruga. Si el rodillo se desgasta más del 110 %, la banda de rodadura se volverá demasiado delgado para ser reconstruida con éxito.
RECONSTRUIBILIDAD
La banda del rodillo y la brida se pueden reconstruir (se emplea una operación de solado) con éxito varias veces si no están desgastadas más allá de los límites de servicio y si se considera el desgaste de la brida central en este punto de servicio. El rodillo generalmente brinda una vida útil igual a la vida útil de la banda de rodadura original hasta los límites respectivos si se sueldan a las dimensiones originales.
PREGUNTAS FRECUENTES (PREGUNTAS Y RESPUESTAS)
¿CADA CUÁNTO TIEMPO ES NECESARIO REALIZAR LA MEDICIÓN DEL DESGASTE DE LOS COMPONENTES?
No existe un tiempo establecido, la realización de las mediciones depende de muchos factores como de variables que no son controlables por el operador como por ejemplo el tipo de suelo y la cantidad de giros que se realicen, un máquina que se encuentra en un suelo sin irregularidades no necesitará realizar la medición de desgaste tan frecuente como una máquina que trabaja en laderas con suelo rocoso o irregular, se debe realizar inspecciones visuales cada vez que sea posible al finalizar el uso del equipo.
Y se debe programar un mantenimiento preventivo en el cual se pueden realizar las mediciones de desgaste, el cual es común realizarse cada 50-100 horas de uso. Como se mencionó con anterioridad en el caso de que las condiciones sean extremas el desgaste aparecerá mucha más rápido, en esos casos es necesario evaluar que lado del tren de rodaje es el más desgastado y evaluar si es factible realizar un cambio de componentes desde un lado a otro hasta lograr que el desgaste de ambos sea igual o si simplemente las piezas necesitan ser reemplazadas.
0 comentarios